May 1, 2024
Enhancing Flowback and Production: The Critical Role of Valves Efficiency and Reliability
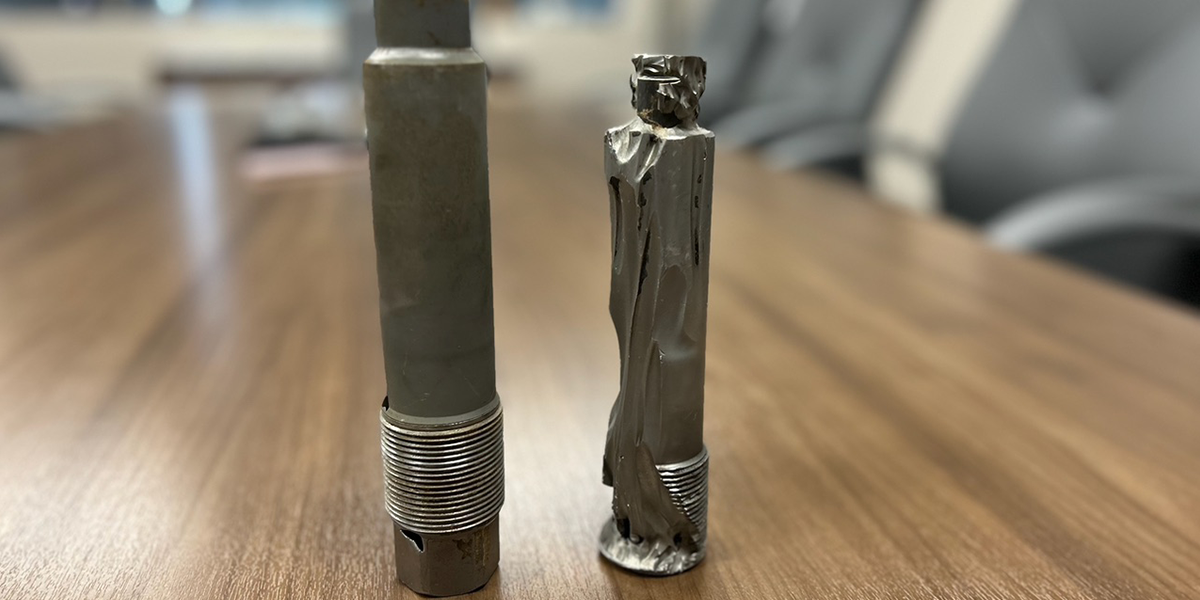
In the complex landscape of oil and gas production, every component plays a vital role in ensuring operational efficiency and reliability. Among these components, valves are critical for the entire scope of flowback and production. From controlling fluid flow rates to maintaining system integrity, valve efficiency and reliability are paramount for optimizing performance and maximizing productivity in the oil and gas industry. Valves serve as the primary control points for regulating fluid flow within production systems. Whether managing flow rates during flowback operations or directing hydrocarbons through production pipelines, valves play a central role in ensuring fluid movement occurs smoothly and efficiently.
Valve damage can lead to operational disruptions, safety hazards, and costly repairs. To mitigate these risks, it is essential to implement a comprehensive set of preventive measures for preventing valve damage. Below are some best practices.
Material Selection: Choosing the right materials for valves is crucial to their performance and durability. In environments with corrosive elements or extreme temperatures, selecting valves made from appropriate materials is imperative. It is critical to consider factors such as fluid properties and flow rates, pressure ratings when choosing valves to ensure optimal performance and longevity. This proactive approach significantly contributes to preventing premature wear and tear.
Environmental Considerations: Environmental factors such as temperature, humidity, and exposure to elements must be considered when designing valve installations. Tailoring preventive measures to the specific conditions of the environment enhances the resilience of valves against external stresses.
Proper Installation: The foundation of valve longevity lies in proper installation. Valves must be installed according to manufacturer specifications, and only qualified personnel should undertake this task. Adhering to installation guidelines ensures that valves function within their intended parameters, minimizing the risk of damage due to incorrect placement.
Monitoring and Inspection: Implementing a robust monitoring system allows for real-time tracking of valve performance. Regular inspections should be conducted to identify any signs of wear, erosion, or corrosion. Early detection through monitoring and inspection enables timely intervention, preventing potential damage and maintaining the integrity of the entire system.
Regular Maintenance: Routine, proactive maintenance is the cornerstone of valve health. Establishing a regular schedule and following the recommended guidelines by the manufacturer for inspection and lubrication ensures that valves are operating optimally. During maintenance checks, professionals should be vigilant for signs of leaks, corrosion, and wear. Addressing minor issues promptly can prevent them from escalating into major problems.
Pressure and Temperature Control: Valves should operate within their specified pressure and temperature limits. Deviating from these limits can lead to accelerated wear and compromised performance. Installing pressure relief valves adds an extra layer of protection, ensuring that valves are shielded from overpressure scenarios.
Corrosion Prevention: Corrosion is a problem across all materials in oil and gas. Cladding material or providing protective coatings can protect flange connections and internals. A solids separation system is also a way to protect equipment before material enters the system. These measures act as a shield, extending the lifespan of valves and minimizing the risk of damage.
Emergency Shutdown Systems: In the face of unforeseen emergencies, swift action is crucial. Installing emergency shutdown systems enables the rapid closure of valves, preventing further damage and safeguarding the entire system. These systems serve as a proactive defense mechanism against potential disasters.
Valve Automation: Minimizing the risk of human error can be achieved through the use of automated valves. Automation not only reduces the likelihood of mishandling but also improves response time in critical situations. Investing in automation aligns with the industry's shift toward technological advancements for enhanced operational efficiency.
Documentation and Record-Keeping: Maintaining detailed records of valve maintenance, inspections, and repairs is essential. This documentation serves as a valuable resource for tracking the lifespan and performance of valves. It aids in decision-making processes related to replacements or upgrades, contributing to the overall longevity of the system.
Training and Education: The human factor is critical in preventing valve damage. Providing comprehensive training to personnel on proper valve operation and maintenance procedures is essential. Operators must be well-versed in the consequences of incorrect valve handling, fostering a culture of responsibility and diligence.
Training on Emergency Procedures: Ensuring that personnel are well-trained on emergency shutdown procedures is fundamental. In high-stakes situations, the ability to execute emergency protocols efficiently can be the difference between minimal damage and a significant incident. Training programs should emphasize the importance of quick and decisive actions to mitigate risks.
Safeguarding valves requires a multifaceted approach encompassing proper installation, regular maintenance, optimal material selection, regular monitoring, and ongoing training. By adopting these best practices, industry professionals can fortify their systems against valve damage, ensuring longevity, reliability, and sustained operational excellence.